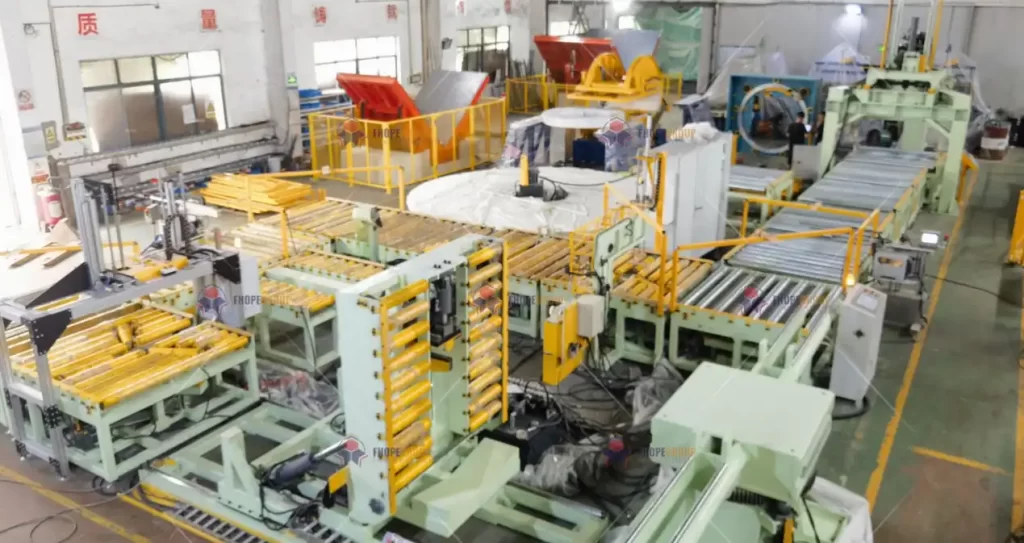
Automatic Coil Packing Line
Automatic coil packing line can be used to pack cable coil, wire coil, steel coil and hose coil. We use different types of conveyors to connect the packing line with the production line for highest efficiency.
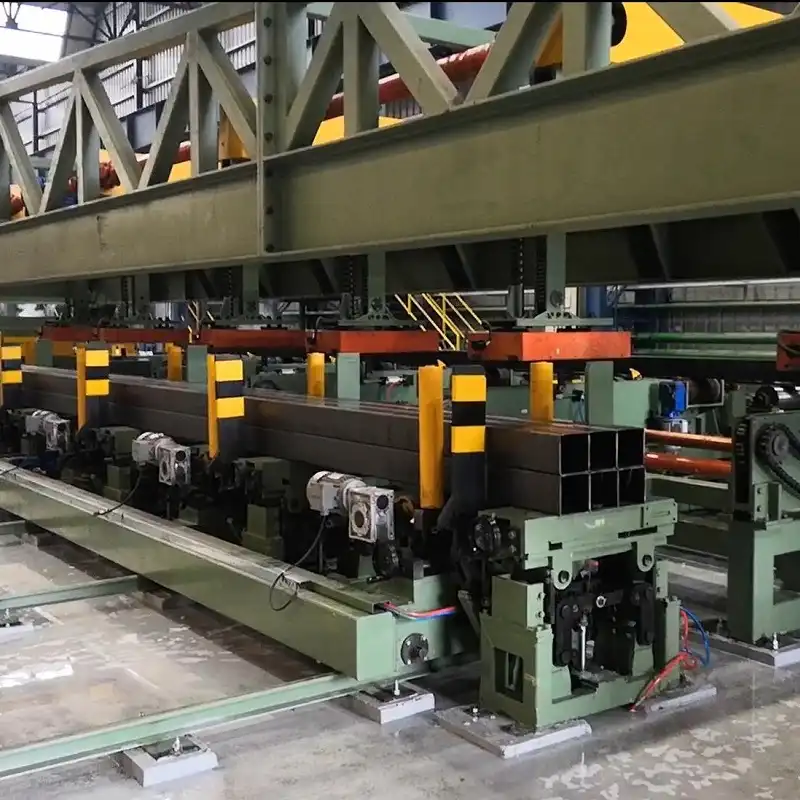
Automatic Steel Tube Packing Line
Automatic steel tube packing line includes differernt solution per packing requirement. There are bagging solution for the stainless steel tube, Automatic steel tube bundle packing line for steel tube mill. And the solution can be mechanical or Megnet stocker.
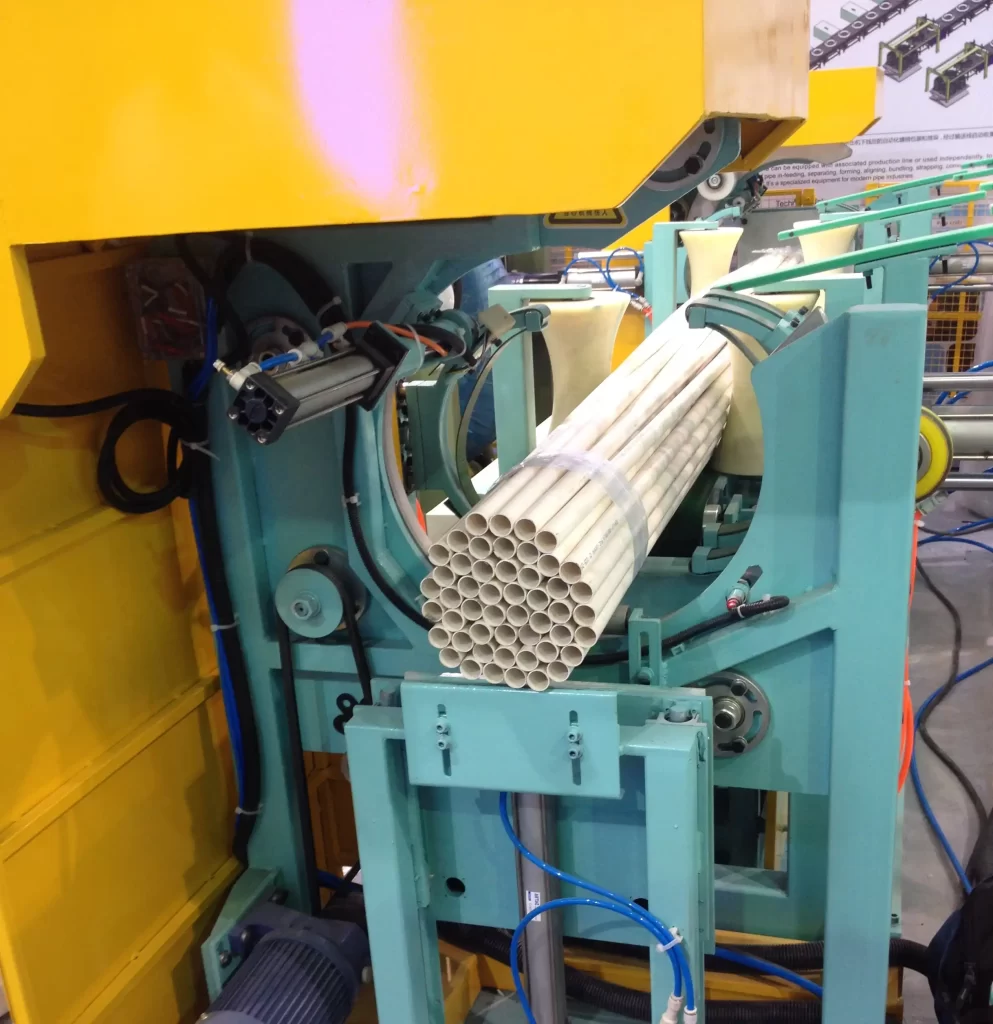
Plastic Pipe Packing Line
Fhope provides different automated pipe bundling and bagging machines for plasitc pipe packaging goal. That is a versatile solution for efficiently packaging solution for PVC and PPR pipes. The system can operate as a standalone unit or seamlessly integrate into a pipe production line.
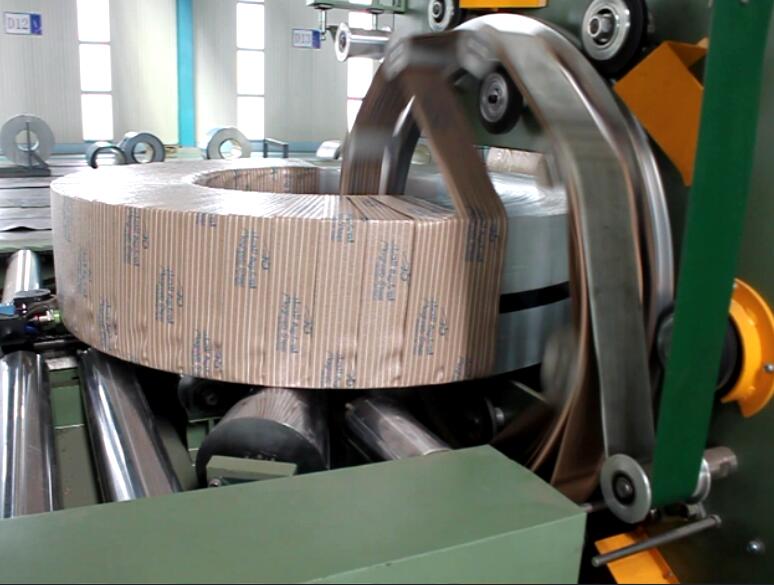
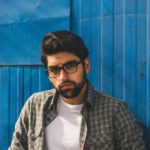
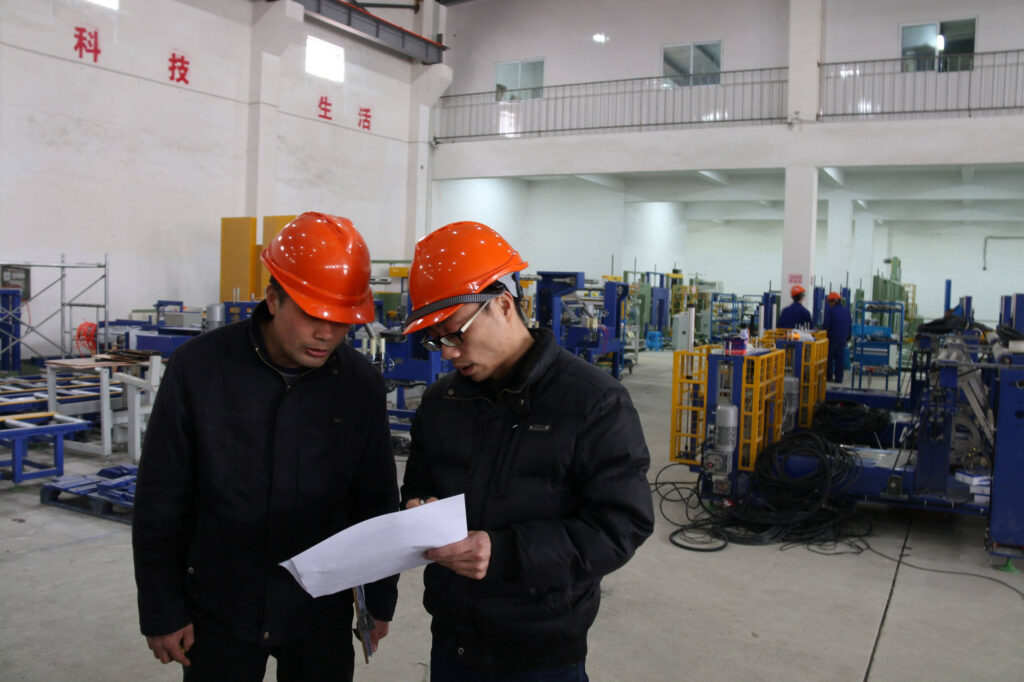
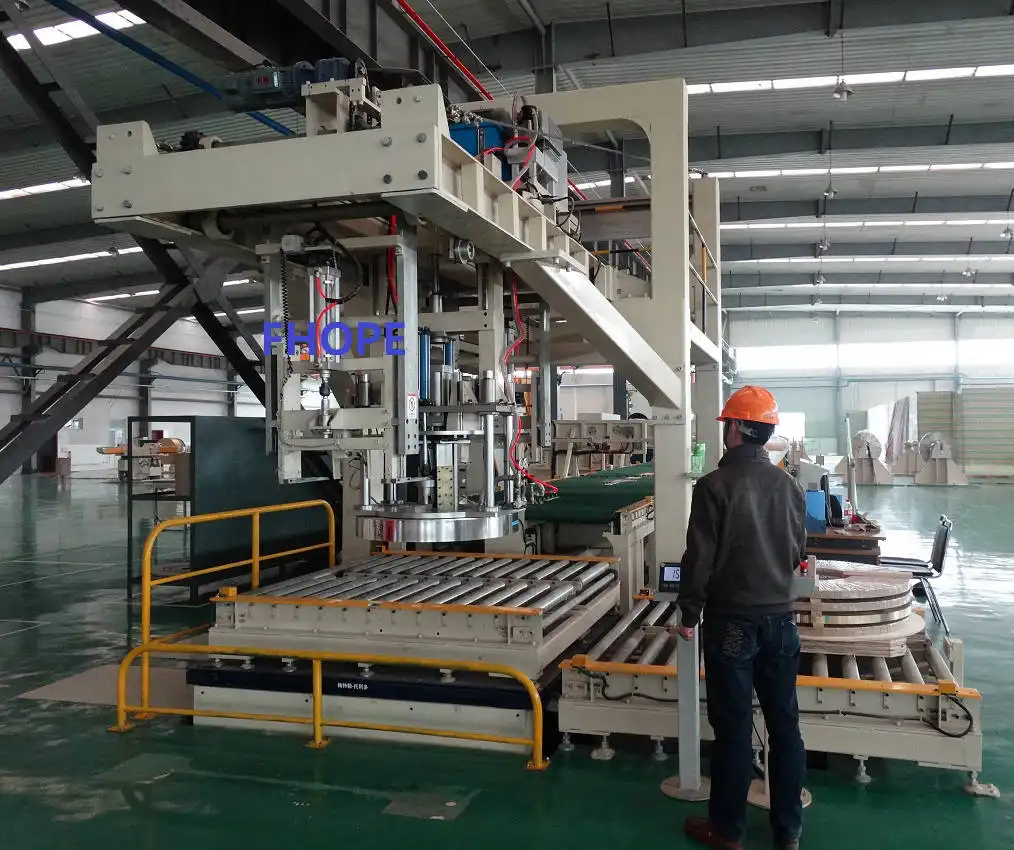